Customization Options in Clean Room Wall Panels for Industry-Specific Needs
- Lucky Deep
- Apr 10
- 2 min read
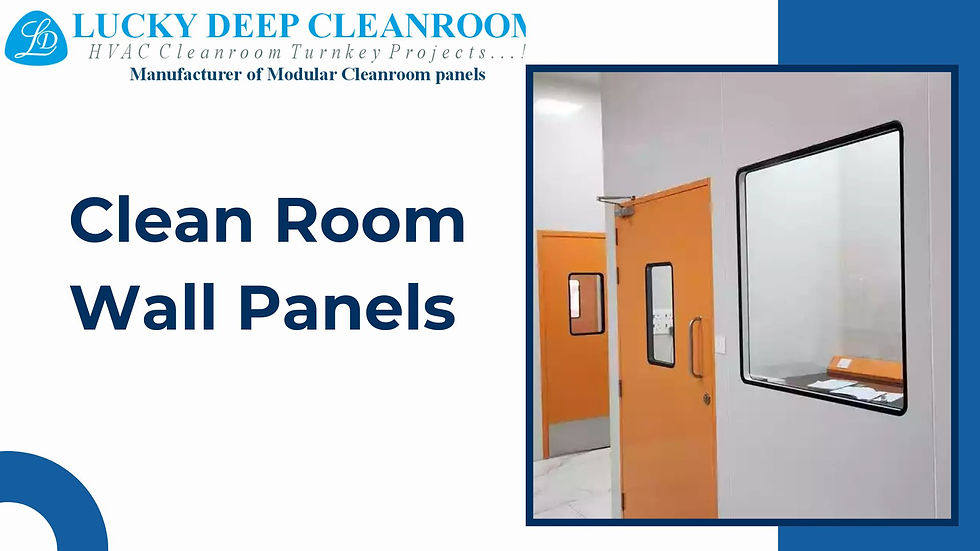
When it comes to building high-performance cleanrooms, Clean Room Wall Panels are one of the most critical components that ensure cleanliness, durability, and compliance with stringent industry regulations. With the rising demand for controlled environments in sectors like pharmaceuticals, biotechnology, electronics, and healthcare, customization has become key to optimizing performance while meeting specific operational needs.
The Importance of Customization in Clean Room Wall Panels
Each industry has unique requirements when it comes to cleanliness, thermal insulation, fire resistance, and chemical stability. That’s why customizable Clean Room Wall Panels offer an effective and flexible solution. From skin material to insulation density, every aspect can be tailored to suit the functional and regulatory needs of different industries.
Key Customization Options Available
Here are some of the most critical customization features that make Clean Room Wall Panels adaptable to industry-specific requirements:
1. Skin Material Combinations
Choose from a variety of surface skins including:
PCGI / PCGI (GPSP)
PPGI / PPGI
SS / SS
These combinations provide flexibility in aesthetics, corrosion resistance, and cleanability—making them suitable for environments with strict hygiene protocols.
2. Sheet and Coating Thickness
Sheet Thickness: 0.5 mm, 0.6 mm, and 0.8 mm
Powder Coating Thickness: 60–80 microns
Pre-Coating Thickness: 30–35 microns
The right thickness ensures strength and resistance to wear and tear, extending panel life even in high-use areas.
3. Insulation Options
Depending on thermal and acoustic needs, select from:
PUF: 40±2 kg/m³
PIR: 48±2 kg/m³
ROCKWOOL: 96 kg/m³ & 144 kg/m³
These materials not only offer excellent insulation but also contribute to fire resistance and soundproofing where required.
4. Panel Dimensions and Layout Flexibility
Standard Width: 1200 mm (custom sizes available)
Height & Panel Thickness: Based on room layout (35, 50, 80, 100 mm options)
Whether it's a compact lab or a full-scale manufacturing facility, these panels are engineered to fit seamlessly into any architectural design.
5. Progressive vs. Non-Progressive Panel Types
Progressive Panels are ideal for permanent structures.
Non-Progressive Panels allow for easy removal and relocation, offering flexibility for dynamic or growing facilities.
6. Sealant and Finishing
Food-grade silicon sealant is applied on both sides for safety and hygiene.
Gap tolerances are kept under 4 mm to ensure a contamination-free setup.
Standard RAL 9002 color available, with additional RAL color options for brand consistency or specific aesthetic needs.
Built for Compliance and Performance
Our Clean Room Wall Panels are supported by powder-coated base runners and interconnecting profiles for maximum stability and cleanliness. Designed with industry standards in mind, they ensure a contaminant-free environment that meets GMP and ISO cleanroom classifications.
Conclusion
As industries continue to evolve, so do the demands for specialized cleanroom environments. The ability to customize Clean Room Wall Panels down to the last detail is what makes them indispensable for any controlled facility. Whether you’re designing a pharmaceutical production space or an advanced electronics lab, tailor-made wall panels provide the foundation for efficiency, safety, and compliance.
Comments